Achieving Welding Quality: Unveiling the Keys of WPS Implementation and Optimization
In the world of welding, accomplishing quality is a quest that rests on the precise execution and optimization of Welding Procedure Requirements (WPS) These foundational papers function as the backbone of welding procedures, dictating the specifications and procedures necessary for generating top quality welds constantly. However, the tricks to opening the full capacity of WPS exist not just in understanding its value but likewise in understanding the intricacies of its application and optimization. By diving right into the crucial elements, approaches, challenges, and finest techniques related to WPS, a world of welding excellence awaits those that are eager to explore its depths.
Importance of WPS in Welding
The Significance of Welding Procedure Requirements (WPS) in the welding sector can not be overemphasized, working as the backbone for ensuring consistency, quality, and security in welding operations. A WPS supplies in-depth directions on exactly how welding is to be executed, consisting of crucial variables such as products, welding procedures, joint layout, filler metals, preheat and interpass temperature levels, welding currents, voltages, travel rates, and more. By adhering to a distinct WPS, welders can keep harmony in their job, causing constant weld high quality across different projects.
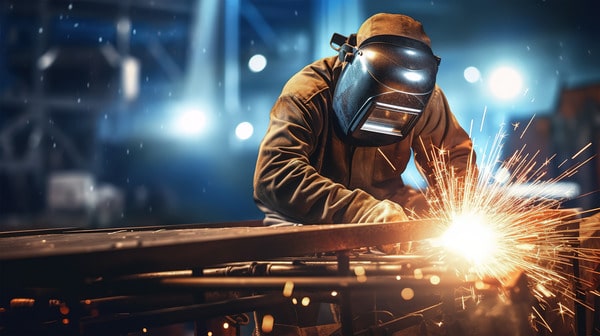
Crucial Element of WPS
Reviewing the essential elements of a welding procedure specification (WPS) is vital for comprehending its function in welding operations. One important element of a WPS is the welding process specification, which describes the specific welding processes to be used, such as gas tungsten arc welding (GTAW) or secured steel arc welding (SMAW) By including these crucial aspects into the WPS, welding procedures can be standardized, making certain top quality, performance, and security in welding operations.
Strategies for WPS Optimization

Second of all, training and credentials of welding employees according to the particular demands of the WPS is vital. Giving comprehensive training programs and guaranteeing that welders are accredited to implement treatments laid out in the WPS can lead to higher high quality welds and minimized rework.
In addition, leveraging modern technology such as welding software and monitoring systems can aid in optimizing WPS. These tools can assist in tracking variables, guaranteeing parameters are within specified limitations, and offering real-time comments to welders, enabling them to make immediate adjustments for improved weld quality.
Common Challenges and Solutions
Encountering barriers in executing the techniques for WPS optimization click this can hinder welding procedures' effectiveness and quality. One usual difficulty is insufficient training or understanding of the welding procedure specifications (WPS) amongst the welding group.
Another obstacle is the absence of proper documents and record-keeping, which is necessary for WPS optimization. Without clear records of welding criteria, products used, and examination results, it becomes difficult to identify locations for enhancement and ensure uniformity in welding processes. Carrying out a durable paperwork system, such as digital welding monitoring software, can aid improve record-keeping and promote data evaluation for constant renovation.
Furthermore, irregular welding equipment calibration and upkeep can try this site pose a considerable challenge to WPS optimization. Routine tools checks, calibration, and maintenance timetables should be complied with purely to guarantee that welding criteria are accurately managed and kept within the specified resistances (welding WPS). By addressing these typical obstacles with proactive services, welding procedures can enhance effectiveness, top quality, and overall welding excellence
Finest Practices for WPS Execution
To guarantee effective WPS execution in welding operations, adherence to industry requirements and thorough attention to detail are vital. When launching WPS implementation, it is important to begin by extensively understanding the particular welding demands of the job. This requires a comprehensive review of the welding procedure specs, products to be bonded, and the ecological problems in which the welding will certainly take place.
Once the requirements are clear, the next step is to choose the proper welding treatment that straightens with these requirements. This entails speaking with the relevant codes and requirements, such as those supplied by the American Welding Society (AWS) or the International Company for Standardization (ISO), to make certain conformity and quality.
Moreover, recording the whole WPS application procedure is necessary for traceability and top quality control. Thorough documents need to be maintained pertaining to welding criteria, product preparation, preheat and interpass temperatures, welding consumables used, and any deviations from the original treatment. Normal audits and evaluations of the WPS can assist identify areas for renovation and make certain recurring optimization of the welding process.


Conclusion
To conclude, the application and optimization of Welding Treatment Specs (WPS) is crucial for accomplishing welding excellence. By comprehending the key aspects of WPS, implementing efficient strategies for optimization, attending to usual difficulties, and adhering to best methods, welders can ensure premium welds and secure working conditions. It is critical for professionals in the welding market to focus on the proper application of WPS to boost overall welding performance and attain wanted outcomes.
The Value of Welding Treatment Specifications (WPS) in the welding industry can not be overemphasized, offering as the foundation for ensuring consistency, high quality, and safety and security in welding operations. A WPS offers in-depth guidelines on how welding is to be carried out, including necessary variables such as products, welding procedures, joint design, filler metals, preheat and interpass temperatures, welding currents, voltages, travel rates, and extra. One crucial aspect of a WPS is the welding process spec, which details the certain welding procedures to be made use of, such as gas tungsten arc welding (GTAW) or secured steel arc welding (SMAW) By including these vital elements into click this link the WPS, welding procedures can be standardized, guaranteeing high quality, effectiveness, and security in welding operations.
It is crucial for specialists in the welding sector to focus on the appropriate application of WPS to improve general welding performance and achieve desired outcomes.